The IoT Platform for Equipment Manufacturers
From Maintenance to Optimization: Boost After-Sales Revenue and Customer Relations with IIOT DataReader.
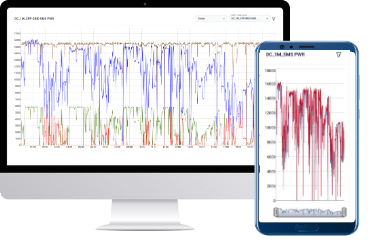
How Can IIOT DataReader Transform After-Sales Solutions and Boost Revenue for OEMs?
Empower your business to thrive in Industry 4.0 by leveraging data-driven insights with cloud-based IIoT software.
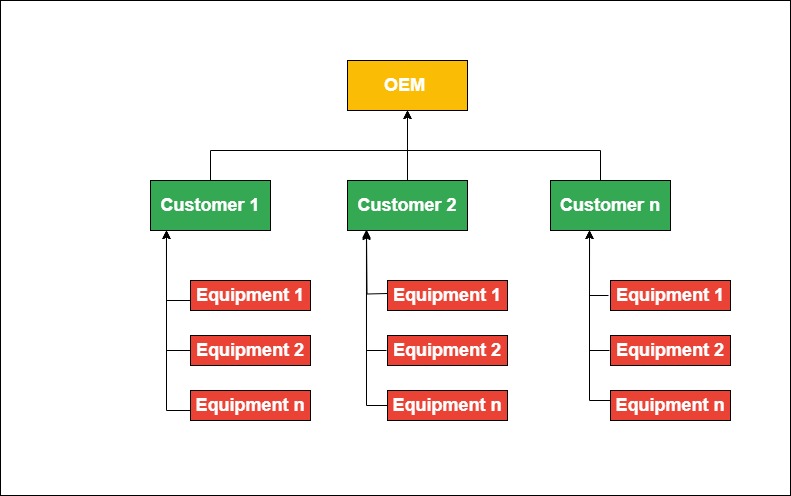
As Shown in the Diagram Above:
•
For OEMs:
Gain full visibility into all connected equipment across your
entire customer portfolio, enabling streamlined monitoring and
proactive management.
•
For the Customers of OEMs:
Allow your customers to monitor their equipment's Performance,
Health, and Historical Data Insights with read-only access
through the IIOT DataReader platform.
Prepare to Wow Your Customers.
Offer Subscription-Based Customer Portals and Increase Your Revenue
Empower your customers with a subscription-based customer portal that delivers real-time equipment insights, advanced maintenance features, and valuable reports. With IIOT DataReader, you can:
Provide Secure Access:
Allow customers to monitor their equipment's performance
and health with read-only access. (Anywhere, Anytime)
Share Valuable Reports:
Offer detailed performance and maintenance reports to help
customers make informed decisions.
Enhance Customer Satisfaction:
Build trust and transparency by giving customers full
visibility into their equipment data.
Enable Smart Maintenance:
•
Preventive Maintenance:
Customers can track their equipment's parts, including
expired parts, due parts, and upcoming expiring and due
parts, ensuring timely maintenance.
•
Predictive Maintenance:
Customers receive predictive alerts categorized as High,
Medium, or Low for their equipment’s parts, helping them
address potential issues before they occur. They can
also access the history of predictive alerts for better
decision-making.
•
Comprehensive Maintenance Log History:
Customers can view the complete maintenance log of their
equipment’s parts, providing a clear record of all
performed maintenance activities.
Empower Your Customers with the Tools They Deserve.
Shift from Reactive to Proactive Maintenance: Boost After-Sales Revenue with IIOT DataReader
IIoT Data Readers empower OEMs to transition from a reactive, cost-driven service model to a proactive, customer-centric approach.
By leveraging the power of data and technology, OEMs can significantly improve customer satisfaction, reduce costs,reduced downtime, improved customer service, increase revenue, and gain a competitive edge in the market.
Here's how:
Centralized Maintenance Management:
With IIOT DataReader, OEMs can monitor all upcoming preventive maintenance schedules and predictive maintenance alerts across their entire customer base. Whether you're in the factory or working remotely, gain instant access to critical maintenance data anytime, anywhere.
Real-Time Predictive Maintenance Alerts:IIOT DataReader provides real-time predictive maintenance alerts categorized by priority—High, Medium, or Low. This enables OEMs to address potential issues proactively, reducing the need for frequent site visits and lowering operational costs.
Historical Predictive Alerts and Maintenance Logs:OEMs can view the history of predictive alerts for each part, offering insights into past performance and potential recurring issues. These historical data points help OEMs identify trends and make more informed decisions for future maintenance.
Additionally, OEMs can access detailed maintenance logs for every part, allowing them to track all maintenance activities over time, such as repairs, replacements, and actions taken. This history enhances decision-making and ensures accountability.
Maintenance Logs Management:Once a part’s preventive maintenance is either expired or due for service, only an OEM’s engineer can clear the preventive maintenance error from the dashboard. This feature ensures that the maintenance process remains transparent and controlled, maintaining the integrity of the data. OEMs have full control over the maintenance workflow to ensure all actions are performed accurately.
Enhanced Customer Communication:OEMs can view all maintenance alerts on a single, unified dashboard. Use these insights to reach out to customers proactively—inform them of upcoming part replacements or repairs and strengthen customer relationships. This approach boosts after-sales revenue through increased service and spare parts sales.
Reduced Service Costs:By leveraging IIOT DataReader's predictive maintenance capabilities, OEMs can reduce machine downtime. Anticipating equipment failures allows service teams to act before breakdowns occur, minimizing emergency visits and cutting aftermarket service costs.
Optimized Service Operations:The IIOT DataReader’s Services Bundle empowers OEMs with:
•
24/7 remote support and monitoring tools
•
The ability to anticipate and resolve equipment issues
remotely
•
Streamlined workflows to manage service operations
efficiently
Increased Revenue Opportunities:
Maintenance insights transform into revenue-generating opportunities. By staying informed about customer equipment needs, OEMs can upsell spare parts or additional services, creating a steady stream of after-sales income.
Industry 4.0 Ready:IIOT DataReader aligns with Industry 4.0 goals, equipping OEMs with data-driven tools to enhance maintenance strategies and embrace smart manufacturing.
Win-Win for both you and your customers:IIOT DataReader not only boosts revenue for OEMs but also reduces service costs, enhances customer satisfaction, and positions your business as a leader in after-sales solutions. With its powerful features, OEMs can transition from reactive maintenance to proactive strategies, creating a win-win for both you and your customers.